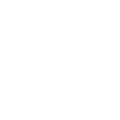
The aim of “Biber” is to provide complete solution for parametric wood work in Rhino + Grasshopper for users who are seeking innovative work flow and looking forward to realize the out of box design.
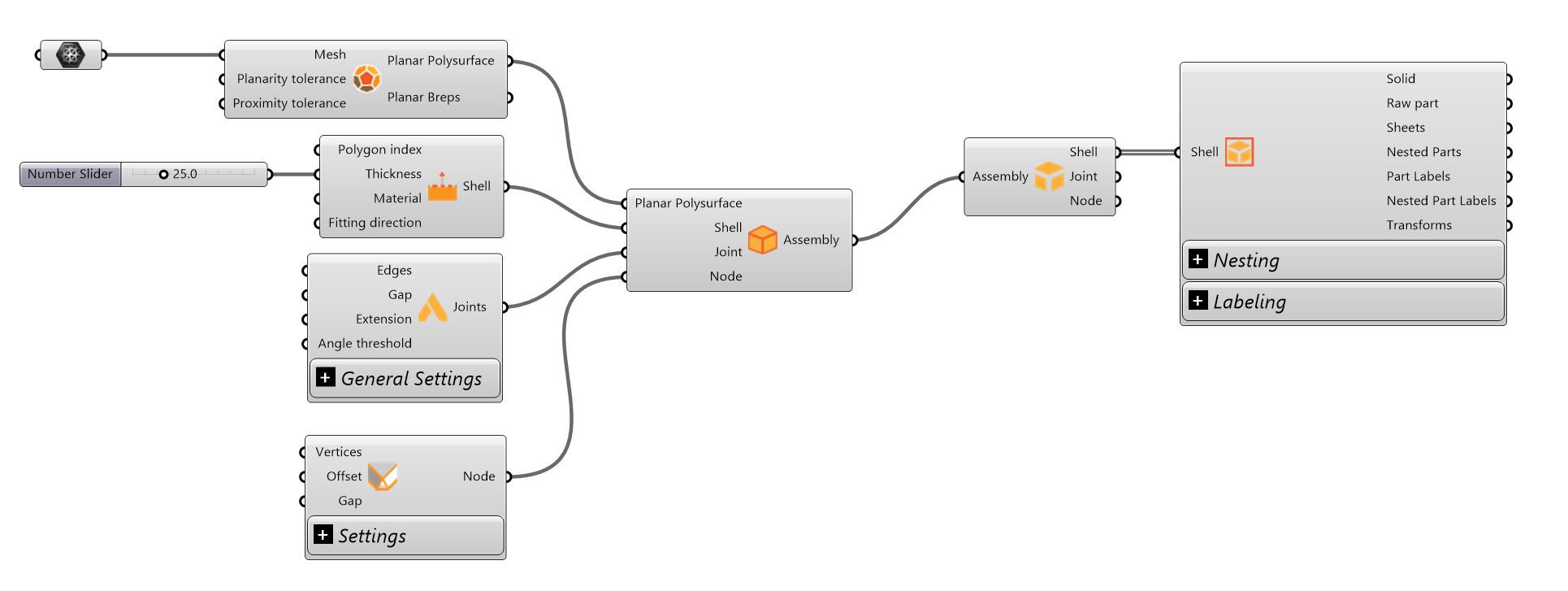
The workflow
Biber offers a simple yet effective workflow to build the parts from geometries with planar sheets. Both Mesh and Brep can be used as input geometry. The geometry first is converted to a special form so called Planar Poly Surface (PPS). This format of geometry is specific to Biber which stores the relations between Faces, Edges and Vertices and carries the tolerances which are used to test the planarity of faces and proximity of the vertices.
From each face in the input PPS a part is created. The geometry of each part is constructed taking into account the adjacent parts along the edges and vertices. In order to perform this complex task Biber takes the user input with regards to all components in PPS : Faces, Edges and Vertices. The geometric and topologic information in PPS and user inputs on Shells, Joints and Nodes comes together in an Assembly. The “Biber” assembly is then used to generates the parts or simulate the assembly process.
Once an assembly is successfully created, user can disassemble it. The “Disassemble” component is in fact the main component which takes the most computation power in the entire workflow. After a successful run of Disassemble component , up to three different outputs may be generated. The main output contains the Shell(s) which are used to produce the actual parts. At last user can use “Unfold” to generate the final geometries from each Shell object. The same component allows user to quickly nest the parts into given sheets.
Buy Biber
License Types
We offer various license types for Biber , catering to different needs and durations. Before choosing the most suitable license for your requirements, let us introduce you to the available options:
IMPORTANT NOTICE
Always download latest version of Biber.
Please remember that all licenses will not be renewed automatically. To continue using Biber beyond the license’s expiration date, users must renew their licenses before that time.
Additionally, we highly recommend considering the Professional License or licenses with longer durations, as we may introduce more features to the software in the future. Purchasing a longer-duration license ensures you have access to these new functionalities without incurring any additional costs.
Learn Biber
Version Log
Version 1.0.1.0
Initial version released on 2022-06-12
Version 1.0.2.0 (test version)
In progress . (Beta) released on 2022-08-10
Version 1.1.0.0
In this update a new group of components is added to provide various functionalities with regards to building sub-structures. These components can generate additional elements to permanently or temporary support the main parts in the assembly.
The main components of Biber are also improved to handle the curve edges.
Additional utility item is added to enable user to mark the edges so that it is easier to assemble.
This update is valid till 2022, 12, 1
Version 1.2.0.0
We have included End-Frame components to generate scaffolding to support and guide the assembly during the installation process.
You will also find some improvements in handling the non-manifold joints.
This update is valid till 2023, 02, 1
Version 1.4.0.3
Here are some of the highlights of this release:
- Compatibility with Rhino 8: Seamlessly integrate Biber with the latest version of Rhino for enhanced performance and efficiency.
- Improved Licensing System: Enjoy a smoother and more reliable licensing process for hassle-free usage.
- Merge Multiple P.P.S Components: Now you can effortlessly join two or more Planar Poly Surfaces into a single component, streamlining your workflow.
- New “Add Feature” Component: Enhance your designs by easily incorporating hinges, dowels, pockets, and more into your parts with the new “Add feature” component.
- Enhanced Building Butt Joints: Build butt joints around complex non-manifold edges with improved precision and efficiency.
- Controlled Part Fitting Direction: Define how mitered joints are constructed to simplify part assembly and improve overall accuracy.
- Custom Lap Joint for Effective Milling: Optimize your milling processes with custom lap joints designed for maximum efficiency.
- Bounding Box Filters: Easily filter vertices, edges, and meshes using bounding box filters for improved selection and manipulation.
Let’s Discuss